Aim: To investigate how different concentrations of sodium chloride affect the rate of corrosion on iron nails.
Theory:
Corrosion is the degradation of a metal due to chemical reactions between it and its surrounding environment (Bell, 2015). It is most commonly associated with rust, in particular the rusting of metals such as iron.
Iron corrosion is a redox reaction and in this reaction, two events occur oxidation and reduction. During oxidation, a substance loses electrons and during reduction, a substance gains electrons that are released from the oxidation process (Wiley, 2002). In order for the corrosion of iron to occur, both oxygen and water must be present as seen in the redox reaction below:
Iron surrounded by the presence of moisture (H2O) begins to lose electrons, thus becoming a cation in solution:
Oxidation reaction: Iron is oxidised (loses e-) (electrons)
Fe(s) → Fe2+ (aq) + 2 e–
The lost electrons are now used to decrease the oxygen dissolved in the water (the water will contain some dissolved oxygen as well as H+ and OH– ions):
Reduction reaction: Oxygen is decreased (gains e-)
O2– (aq)+ 2H2O (aq)+ 4e– → 4OH–
The Fe2+ ions then chemically react and bond with the OH– ions in water to create iron hydroxide, which eventually dries up to form rust: (Iron (III) Hydroxide)
Fe2+(aq) + 2OH–(aq) → Fe(OH)2 (aq) → Fe2O3 (s) (rust)
The factors that will speed up the rate of corrosion include an increase in: the amount of oxygen, temperature, chemical salts, humidity and pollutants
Oxygen: In open environments when water comes in contact with an iron object, two reactions start almost instantly. The first is when the water mixes with carbon dioxide in the air to create a weak carbonic acid. Whilst the acid is being formed and the iron is dissolving, some of the water starts to separate into its elements, hydrogen, and oxygen.
The extra oxygen and dissolved iron bond into the ionic compound, iron oxide. On the other hand, in submerged environments, if an electrolyte (conducting solution) comes in contact with an area of metal comprising of more oxygen than the electrolyte in contact with a different area of the metal, then the higher oxygen-concentrated area becomes targeted and results in accelerated corrosion (Capital Painting, n.d).
Temperature: Since the process of corrosion is electrochemical in nature, increasing the temperature usually also increases the rate of corrosion. This is because if you heat a substance, the particles move quicker and so collide more frequently (Clark, 2002). Consequently, the rate of corrosion speeds up in hotter environments and slows down in cooler ones (Capital Painting, n.d).
Chemical Salts: When in solution, chemical salts hasten the rate of corrosion by improving the efficiency (conductivity – how well it conducts electricity) of the electrolyte (Capital Painting, n.d).
Humidity: A major factor in the rate of corrosion is humidity and time-of-wetness. The duration of time a metal is exposed to enough moisture to initiate the corrosion process relates to the time-of-wetness.
Thus, increased humidity and a greater time of wetness increase the rate of corrosion, providing oxygen is present (Capital Painting, n.d). During the corrosion, process water acts as the solvent for the solute oxygen to dissolve into. Since oxygen can dissolve in water and because there is often a surplus of it, the oxygen reacts with the iron hydroxide as shown below:
4Fe(OH)2 + O2 → 2H2O + 2Fe2O3H2O
Iron hydroxide + oxygen → water + Hydrated iron oxide (brown rust)
Pollutants: When pollutants such as acid rain (a by-product from manufacturing plants), and chlorides (in coastal areas) are exposed to metal, the rate of corrosion is accelerated. For example, acid gases such as (hydrogen sulfide) when present can dissolve in moisture that is in contact with the metal (Capital Painting, n.d).
The rate of corrosion of iron can be slowed in many different methods. These methods include coating the metal, plating with a less reactive metal, galvanizing, cathodic protection, and alloying the metal.
- Painting – Restricts water and oxygen from being able to come into contact with iron, resulting in the inability of rust to be created. However, if any part of the paint is damaged (scratched or chipped), then corrosion can occur since water and oxygen can come into contact with the iron (AUS-e-TUTE, 2014).
- Plating with another metal – Similar to painting, if you plate iron with a less reactive metal such as tin, it prevents oxygen and water from coming into contact with the iron. However, once again if the tin or outside metal is scratched, rust will form.
- Galvanizing – The process of applying a zinc coating to iron or steel. The zinc coating prevents water and oxygen from coming into contact with the metal. Although, unlike the previous method if the surface is scratched or chipped then it creates a new galvanic electrochemical cell:
Zn(s) + Fe2+(aq) → Zn2+(aq) + Fe(s)
In this reaction the iron chemically changes to a solid and soon after zinc ions will then produce a protective coating of zinc oxide or carbonate over the outside of the iron, therefore shielding the iron underneath and reducing the rate of corrosion (AUS-e-TUTE, 2014).
- Cathodic Protection – A sacrificial anode (a piece of reactive metal) such as zinc or magnesium can be attached to iron. The more reactive metal (zinc) sacrifices itself by corroding in preference to the iron. However, sacrificial anodes must be renewed once they have corroded, so that iron can stay protected from corrosion.
- Another form of decreasing the rate of corrosion is by running a low voltage electrical current through the iron that you are trying to prevent from rusting. This works by forcing the natural direction of the electrons to flow in the other direction of the system, thus making the electrons unable to start the corrosion process (AUS-e-TUTE, 2014).
- Alloying with Another Metal – Chromium alloyed with iron produces a commonly known alloy known as stainless steel. Once an alloy, the chromium quickly produces an almost impervious layer of oxide which sticks strongly to the surface of the iron, effectively preventing the formation of rust and slowing down the rate of corrosion (AUS-e-TUTE, 2014).
The factor that will be investigated is how higher concentrations of sodium chloride (the independent variable) affect iron nails (the dependent variable) in comparison to distilled water (the control). There will be four beakers with one, three, ten, and thirty percent of sodium chloride along with one beaker with only distilled water which will be the control.
In order to make this a fair test the same volume of solution will be added to each beaker, all the beakers will be kept at the same temperature (room temp), and there will be two trials (one backup set) of each beaker to ensure that the first set of beakers weren’t falsified. The controlled variables will include the temperature, the amount of solution in each beaker, the size of the beakers, the type of beakers, the type of nail, and the size of each nail.
During the process of corrosion, electrons are transferred from one substance to another, that is, the electrons produced from the oxidation of iron (where iron acts as the anode) are transferred to reduce the oxygen, forming hydroxide ions. This is shown in the equations below:
Fe(s) → Fe2+ (aq) + 2 e–
O2– (aq)+ 2H2O (aq)+ 4e– → 4OH–
The electrons from the oxidation of iron are transferred to the oxygen and the redox reaction occurs; there must be both oxidation and reduction reactions.
Salt dissolved in the water produces sodium and chloride ions NaCl → Na+ + Cl–and the presence of these charged particles (ions) greatly improves the capability of the electrolyte to carry ions and accelerates the rate of corrosion. The greater the concentration of sodium chloride, the more ions in the solution and henceforth allowing more redox reactions to occur.
Electrons move far more easily in saltwater due to the presence of ions and since rusting is essentially the movement or transfer of electrons, the presence of these ions allows for a faster rate in the transfer of electrons and so more rapid corrosion. Thus it can be hypothesised that higher concentrations of sodium chloride will increase the rate of corrosion
Hypothesis: It was hypothesized that if the iron nails were placed in higher concentrations of saltwater then the nail in the strongest concentration of sodium chloride would have the highest rate of corrosion and thus corroding more quickly than the nails in lower concentrations.
This is because the higher concentrations of sodium chloride contain more ions (Na+ Cl-) that assist in transferring cations and anions through the electrolyte (the solution) which speeds up the corrosion rate of iron, which involves the transfer of electrons. The electrons produced from the oxidation of iron are transferred to oxygen in reduction.
Apparatus:
Equipment | Quantity |
Small Test Tubes | 10 |
20 mL of distilled water | 1 |
20mL NaCl 1% solution | 1 |
20mL NaCl 3% solution | 1 |
20mL NaCl 10% solution | 1 |
20mL NaCl 30% solution | 1 |
Iron Nails | 10 |
Labels | 10 |
Steel wool | 1 |
Sticky Tape | 1 |
Small Test Tube Rack | 1 |
Measuring Cylinder | 1 |
Procedure:
- Lab coats, goggles, and gloves were worn throughout the experiment.
- All equipment was collected as per the apparatus list.
- The iron nails were fully polished with the steel wool
- One nail was placed inside each of the small test tubes
- All of the small test tubes were placed in the test tube rack
- 10mL of 0% sodium chloride solutions were measured in a small measuring cylinder and then poured into the test tube.
- Step 6 was repeated 9 times for 1,3,10 and 30% sodium chloride solutions plus for the second trial
- Observations of the initial physical condition of the nail were recorded in a data table.
- Labels were made for each of the test tubes in accordance with their concentration of the salt solution and trail number.
- Labels were put onto the small test tubes
- The experiment proceeded at room temperature for nine days. Observations were made on days 0, 2, 3, 6, 7, and 9.
Data Collection:
Corrosion Rating Key
0 = No rust present at all. Solution is clear and colourless with no precipitate. No particles in suspension.
1 = Minimal signs of rust on the nail. Solution is clear and colourless with no precipitate. No particles in suspension.
2 = Some signs of rust on the nail. The solution is clear and with a tinge of orange-yellow with no precipitate. Some particles in suspension but barely noticeable.
3 = Partially covered with rust on the nail. Signs of precipitate and solution is yellowish orange. Some particles in suspension which is very noticeable.
4 = Almost half of the nail is covered in rust. Some orange precipitate found in the test tube. The solution has a yellowish–orange tinge. Orange particles are in suspension.
5 = Half of the nail is covered in rust. The orange precipitate is evident and dominant at the bottom of the test tube. The solution has a definite yellowish–orange tinge. The solution is cloudy with orange particles in suspension.
6 = Nail is covered by a substantial amount of rust and covers more than half of the nail. The solution is orange with hints of yellow. Brown precipitate covers the bottom of the tube. The solution is cloudy with brown particles in suspension.
7 = Nail is mostly covered by rust. The solution is clear and has a definite orange color. Dark brown precipitate covers the bottom and is thick. The solution is cloudy with dark brown particles in suspension.
8 = Almost fully rusted all over the entire nail with signs of the original metal. The solution is cloudy with dark brown particles in suspension. Dark brown principate layers the bottom of the test tube and is building up.
9 = Almost fully rusted all over the entire nail with minimal signs of the original metal. . Solution is cloudy with dark brown particles in suspension. Dark brown principate layers the bottom of the test tube and is building up.
10 = Completely rusted all over the entire nail with no signs of the original metal. . Solution is cloudy with dark brown particles in suspension. Dark brown principate layers the bottom of the test tube and is building up.
NaCl concentration %
| Days | |||||
2 | 3 | 6 | 7 | 9 | ||
Control 0% NaCl | 3 | 3.5 | 5 | 5.5 | 5.5 | |
1% NaCl Solution | 3 | 3.5 | 3.5 | 6 | 6 | |
3% NaCl Solution | 3 | 4 | 4 | 6 | 6 | |
10% NaCl Solution | 3.5 | 4 | 4 | 7 | 7.5 | |
30% NaCl Solution | 2 | 2.5 | 2.5 | 2.5 | 2.5 |
Data Analysis
Graph 1 : Corrosion rating vs. Time
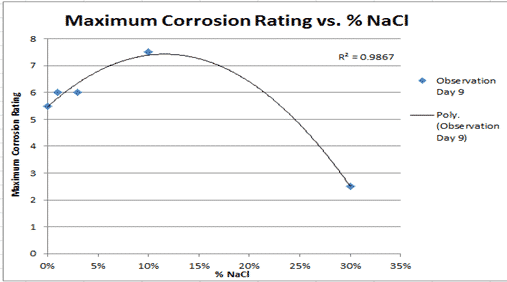
Let section 1 be anything on the x axis from 0 to 3, and anything on the y axis from 0 to 4.
Let section 2 be anything on the x axis from 6 to 9.5, and anything on the y axis from 2 to 6.
Graph 2: Maximum Corrosion Rating vs. % NaCl
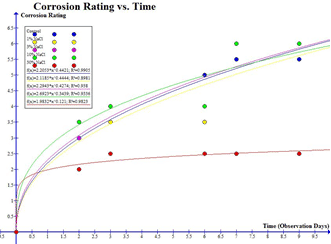
Let section 1 be anything on the x axis between 0% and 10% and anything on the y axis from 5.5 to 7.5.
Let section 2 be anything on the x axis between 10% and 30% and anything on the y axis from 7.5 to 2.5.
The gradient of each section in each graph can be calculated by:
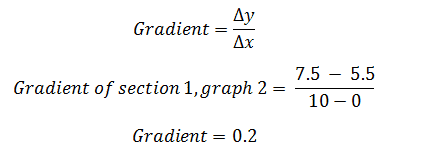
Therefore the gradient for section 1, graph two equals 0.2. This was repeated for each line and section per graph:
Graph | Section | Line | Gradient |
1
| 1 | 1 (Control) | 1.1666666666667 |
2 (1% NaCl) | 1.1666666666667 | ||
3 (3% NaCl) | 1.3333333333333 | ||
4 (10% NaCl) | 1.3333333333333 | ||
5 (30% NaCl) | 0.8333333333333 | ||
2 | 1 (Control) | 0.1666666666667 | |
2 (1% NaCl) | 0.8333333333333 | ||
3 (3% NaCl) | 0.6666666666667 | ||
4 (10% NaCl) | 1.1666666666667 | ||
5 (30% NaCl) | 0.0000000000000 | ||
2 | 1 | 1 | 0.2000000000000 |
2 | 1 | -0.2500000000000 |
In order to calculate the percentage error in the R2 values the following formula will be used:
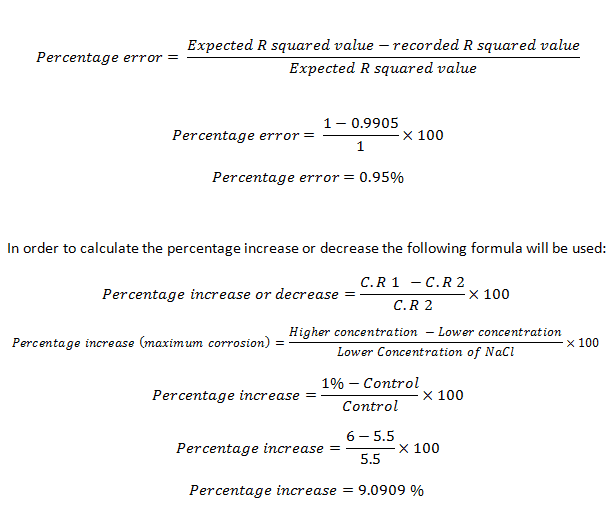
Discussion
Graph 1 demonstrates a power relationship between the corrosion rating and the time (observation days). This power relationship was the same for each line (independent variable) and can be proven by the R2 value for all the lines which was above 0.89. It can further be demonstrated as all the other lines which didn’t have a power relationship, had R2 values lower than what was graphed.
The recorded results all represent R2 values which were 11 percent or less than the expected result of 1.00. This means that either there was an experimental error or errors or that the amount of corrosion on an iron nail and the time (days) can’t be graphed mathematically correct. For the control it can be seen that the R2 value is 0.9905, which is 0.95 percent off the expected result, demonstrating that there was virtually a perfect fit for all the points on the line.
Contrary to this accuracy and precision, the one percent solution of sodium chloride had an R2 value of 0.8981, which is an anomaly in comparison to the rest of the other R2 values in graph 1, which can further be demonstrated as it was 10.19 percent off the expected result. For the three percent solution of sodium chloride, it had an R2 value of 0.938 which is quite accurate being only 6.2 percent off the expected result.
Following the same accuracy as the one and three percent sodium chloride solutions, the 10 percent sodium chloride solution had an R2 value of 0.9336. This also shows a very accurate result as it was 6.64 percent off the expected result. Lastly, the 30 percent solution of sodium chloride had the second most accurate and precise R2 value with 0.9823. This demonstrates that it was only 1.77 percent off the expected result and that there was an almost perfect fit for all the points on the line.
The power relationship in graph 1 illustrates that for all the independent variables except for the 30 percent solution of sodium chloride solution, the amount of corrosion on the iron nails, according to the corrosion rating key, increased overtime proving the expected positive gradient. However, for the 30 percent sodium chloride solution the line remained relatively flat, thus meaning that the nail in the 30 percent sodium chloride solution rusted the least.
In graph 1, section one the gradient of both the control and the 1 percent sodium chloride solutions were 1.6 recurring. This means that there is not much difference in the rate of reaction at the start of the experiment.
The gradients for both the 3 percent and 10 percent sodium chloride solutions were 1.3 recurring also demonstrating that at the beginning of the experiment there was not much difference in the rate of reaction, however, this would most likely be considered an anomaly due to the large percentage difference between the two concentrations.
The gradient of the 30 percent sodium chloride solution was 0.8333333, illustrating that there was a slow rate of reaction at the beginning. In section two of graph 1, it can be seen that there is a much wider range of results. The gradient of the control in section two stayed the same; however, the gradient of the 1 percent sodium chloride solution decreased to 0.8333, a 50 percent drop in reaction rate.
As for the gradient of the 3 percent sodium chloride solution, the gradient was 0.6 recurring in section 2, there was also a 50 percent drop in reaction rate. For the 10 percent sodium chloride solution the gradient in section 2 was 1.16 recurring, which was a decrease of 12.5 percent in the reaction rate. The gradient of the 30 percent sodium chloride solution in section 2, was 0 and so it had a decrease of 100 percent, and so as a result the corrosion rating stayed the same each observation day as there was no reaction happening.
Graph 2 demonstrates a polynomial relationship between the maximum corrosion and the percentage of sodium chloride solution. This polynomial relationship can be proven by the increase and decrease of the maximum corrosion rating over the percentage of sodium chloride solution. It can also be proven by the R2 value which was 0.9867 meaning that there was almost a perfect fit for all the points on the line. The R2 value was extremely precise and accurate as it was only 1.33 percent off the expected R2 value of 1.
The polynomial relationship in graph 2 demonstrates a peak at which the most corrosion can occur, and then after that larger concentrations of sodium chloride decrease the rate of corrosion. The polynomial relationship demonstrates that from 0 to 10 percent of sodium chloride the corrosion rating increased over time, thus meaning that the amount of corrosion also increased.
However, after the 10 percent solution of sodium chloride, the low corrosion rating of the 30 percent sodium chloride caused the line to steep down and thus illustrate that the rate of corrosion decreases after the sodium chloride solution close to the 10 percent mark. The cause of the polynomial relationship between the independent and dependent variable in graph 2 is the concentration of sodium chloride that can be dissolved in solution.
Too much sodium chloride decreases the amount of oxygen that can be dissolved in water, thus decreasing the rate of corrosion since when there is too much sodium chloride there not much space for the oxygen in the air to dissolve, and so the reduction process happens slower because there aren’t many oxygen molecules that can be decreased.
Contrary to this enough sodium chloride increases the conductivity of the electrolyte since there are more ions in the solution; which then increases the rate of corrosion. This can be proven as the solubility of oxygen in seawater is between 17 percent and 21% less than that of fresh water at room temperature (Free Drinking Water, n.d)
In graph 2, section 1 the gradient of the line was 0.20, however, in section two of the graph, the gradient was -0.25 as the line began to slope down as previously mentioned by the decreasing corrosion rating after 10 percent solution of sodium chloride. The gradient difference between section and section two was a 10.25 percent difference. Therefore meaning that there was a 10.25 percent difference in the rate of corrosion between 10 and 30 percent sodium chloride solution.
The difference in the maximum corrosion rating for the control and 1 percent sodium chloride solution had 9.09 percent higher corrosion rating. This was expected due to the fact that the control did not contain sodium chloride and so there was no substance to increase the conductivity of the solution. There was no difference in the maximum corrosion rating for 1 and 3 percent sodium chloride solution; this would be considered an anomaly.
The maximum corrosion rating for the 10 percent solution of sodium chloride was a 25 percent increase in the corrosion rating in comparison to the three percent solution of sodium chloride. This would be expected due to the 10 percent solution being extremely close to the optimal percentage of sodium chloride, 11 percent. Lastly, the biggest difference in corrosion rating came from the 10 percent solution of sodium chloride and the 30 percent solution of sodium chloride as there was a negative 66.6 percent decrease in the corrosion rating.
It was a negative decrease due to the gradient of the line being negative. Surprisingly all the trials had the same corrosion rating relative to what they were already recorded as. The only other anomalies were that the 3 percent sodium chloride solution, trial 1 had green rust on compared to trial 2 which had brown rust (what was expected).
It can be found that the green rust formed as a result of the ratio between hydroxide ions formed in the reduction reaction and chloride ions in the solution being higher than 1. Another anomaly was found in graph 1, where the 10 percent and 1 percent corrosion rating on day 6 did not follow the trend pattern of their respective lines. This could have been caused due to an error in the observations and the corrosion rating that it was recorded at.
The errors within our experiment were the corrosion rating and a parallax error in the measuring of the amount of solution. The corrosion rating was an error within the experiment as a large proportion of it was opinion-based and was a qualitative measurement. In order to try and quantify the amount of corrosion on the nail, a corrosion scale was made, which related to the qualitative observations that were recorded.
This error could’ve been improved by more people checking the amount of corrosion on each nail so that there is less bias. Another way corrosion rating could’ve been improved is by having more trials and by making an average corrosion rating for each trial. Lastly, it could have also been improved by trying to quantify the amount of rust in each test tube, by weighing the precipitate. The parallax error that was made came from when the solutions of sodium chloride were being poured inside each test tube.
This could’ve been improved by the observers being at the same height of the test tubes to accurately see if 10mL of the appropriate sodium chloride was in each beaker.
The hypothesis was proven to be correct and the iron nails that were placed in higher concentrations of sodium chloride corroded the most; although in both graphs 1 and 2 the 30 percent solution of sodium chloride had a lower corrosion rating compared to all the other independent variables.
This was caused as the large proportion of salt in the solution didn’t improve the conductivity of the solution instead it made it harder for oxygen gas to dissolve in the solution since there was already a large amount of salt that was dissolved. If there were to be a new hypothesis it would be: It was hypothesized that if the iron nails were placed in sodium chloride solution less than 11 percent sodium chloride then the iron nails placed in the highest concentration of sodium chloride would have the highest rate of corrosion and thus would corrode more quickly than the iron nails in lower concentrations of sodium chloride.
In conclusion, the aim was achieved and so it was found that placing iron nails in higher concentrations of sodium chloride corrode the most. However, once iron is placed in concentrations bigger than 11 percent then the rate of corrosion begins to decrease, as seen with the 30 percent sodium chloride solution.
Bibliography:
Bell, T n.d., What Is Corrosion, About.com, accessed 6 August 2015, <http://metals.about.com/od/Corrosion/a/What-Is-Corrosion.htm>.
Jack, T 2007, What are the effects of rust?, University of Illinois, accessed 9 August 2015, <https://van.physics.illinois.edu/qa/listing.php?id=494>.
Why does salt speed up corrosion? 2011, Let Us Find Out, accessed 8 August 2015, <http://www.letusfindout.com/why-does-salt-speed-up-corrosion/>.
Chemistry Tutorial : Corrosion 2014, AUS-e-TUTE, accessed 8 August 2015, <http://www.ausetute.com.au/corrosion.html>.
Redox Reactions 2002, Wiley, accessed 6 August 2015, <http://www.wiley.com/college/boyer/0470003790/reviews/redox/redox.htm>.
Factors that affect the rate of corrosion n.d., Capital Painting, accessed 7 August 2015, <http://www.capital-painting.com/factors-that-affect-the-rate-of-corrosion/>.
Explain which Factors affect corrosion? 2009, eNotes, accessed 7 August 2015, <http://www.enotes.com/homework-help/explain-which-factors-affecting-corrosion-104539>.
9.6 Shipwrecks, Corrosion and Conservation: 5. Rate of decay and corrosion 2003, Charles Sturt University, accessed 25 August 2015, <http://hsc.csu.edu.au/chemistry/options/shipwrecks/2732/ch965Dec2_03.htm>.
How does rust work? n.d., How Stuff Works, accessed 13 September 2015, <http://science.howstuffworks.com/question445.htm>.
Clark, J 2002, THE EFFECT OF TEMPERATURE ON REACTION RATES, Chem Guide, accessed 13 September 2015, <http://www.chemguide.co.uk/physical/basicrates/temperature.html>.
Green Rust n.d., Corrosion Pedia, accessed 16 September 2015, <https://www.corrosionpedia.com/definition/610/green-rust>.
DOES SALT CONCENTRATION OR SALINITY OF WATER AFFECT SOLUBILITY OF OXYGEN? n.d., Free Drinking Water, accessed 16 September 2015, <http://www.freedrinkingwater.com/water_quality/water-science/j-9-08-does-salt-concentration-salinity-water-affect-solubility-oxygen-page2.htm>.
Thank you very much
This was really helpful, thank you so much!